Авиационная фанера что это такое
Авиационная фанера | Использование авиационной фанеры
Авиационная фанера выпускается из шпона березы, являющегося высококачественным, обладает тремя и более слоями, склеенными друг с другом, и при своей сравнительно небольшой плотности имеет отличную гибкость и прочность. Таким образом, авиационный тип фанеры с толщиной от трех до шестнадцати миллиметров или еще больше, может быть использован не только для авиамоделирования, но и для музыкальных инструментов. Наиболее тонкий лист может быть толщиной 1 мм.
Давайте поговорим о том, какие свойства имеет материал для изготовления конструкций, а также какие он имеет марки и где применяется.
Изготовление авиационной фанеры
Данный тип фанеры еще называется дельта-древесиной, что, по своей сути, подобно авиационной, потому что ее изготавливают из точно такого же березового шпона с добавлением пластика. Перед тем как склеить слои бакелитовым клеящим составом их следует пропитать фенолформальдегидной смолой с температурой в 270 градусов и с давлением в шесть атмосфер. Производится данный материал только согласно ГОСТ 226-41, а также имеет сорта А и Б.
Производство и маркировка авиационной фанеры
Таким образом, продукция может быть разделена на несколько марок: БП (А или В) – это касается такого типа фанерных листов, которые клеятся бакелитовой пленкой типа А или В. Существует еще марка БС-1, в которой шпон склеивают с помощью смолы СФЖ-3011 и БПС-1В. Это указывает на то, что до трех миллиметров продукт клеится на бакелитовую пленку с типом B, а дальше уже применяется она же с типом А, но только на наружном слое, а изнутри используется смола.
При производстве фанеры с такой маркировкой необходимо, чтобы шпон был расположен перпендикулярно. Другими словами, по своему направлению волокна каждого слоя пересекаются между собой, чем создают что-то вроде структурной решетки, с помощью которой становится намного больше прочность изготавливаемых конструкций.
Прибавление уровня прочности, касающееся растяжения древесины конструкционного типа прямо зависит от его уменьшающейся толщины и для продуктов с первым сортом составляет 65-95 МПа и вторым – 50-82,5 МПа. Если толщина материала становится меньше, то его предел прочности, наоборот, становится больше. Это касается образования сколов по клеевому слою. Их размер колеблется в пределах 1,6-2 МПа. Наиболее оптимальным уровнем шероховатости поверхности авиационных фанерных листов является величина 100 мкм при уровне влаги 5-9%.
По длине геометрические данные этого вида древесины колеблются в разных пределах от 1000 до 1525 мм, а по ширине от 800 до 1525 мм. Допустимое значение градации составляет двадцать пять миллиметров. Листы с маркой БП (А или В) могут иметь толщину от одного до трех миллиметров, а вот у БС до двенадцати, а у БПС от двух до шести.
Таким образом, форматы фанеры авиационного типа могут иметь размеры: 1550х1550, 1525х1525, 1270х1270, 1220х1220. При всем этом толщина может быть самого различного размера от 0,4 до 12 миллиметров.
Любой тип фанеры изготавливается по инструкции, составленной по ГОСТ 3916.1-96. В листе обязательно должно быть нечетное количество слоев, а волокна располагаются перпендикулярно друг другу с углом в девяносто градусов, образуя при этом структурную решетку. Что касается самого процесса производства таких продуктов, то он имеет несколько определенных этапов. У фанеры маркировка может иметь буквы Ш и Ш2, что говорит о том, что была проведена односторонняя или двусторонняя шлифовка. Фанеру, обладающую низким сортом, не шлифуют, и в маркировке таких материалов обладает буквами НШ.
Применение авиационной фанеры
Уже давным-давно известен тот факт, что данный тип конструкционной древесины широко применяли для строительства самолетов, в особенности, когда шла война. За счет того, что материал обладает сравнительно небольшим весом, автомобиль получался легким, а благодаря гибкости и прочности появлялась возможность выдерживать аэродинамическую нагрузку при эксплуатации самолетов. Хотя, в авиамоделировании, и на сегодняшний день применяется авиационная фанера. Кроме использования в авиационном строительстве такие фанерные листы популярны в коллекционировании (самолеты или суды). Кроме того, данный материал также приобрел широкую популярность в судостроении.
Во время архитектурных происков каких-либо уникальных решений для строительства различных конструкций (здания, города, дома), проектировщиками самостоятельно изготавливаются макеты. На их основании и производится утверждение проектов. К тому же с помощью гибкой фанеры можно воплотить в жизнь нестандартные решения в оформлении интерьера.
Также было бы странно не сказать о том, что из авиационной фанеры производятся музыкальные инструменты. Для их изготовления ранее никак было не обойтись без высококачественных фанерных листов. Для каждого из дековых инструментов требуется применение специальной древесины и за несколько прошлых лет замена пластиком себя никак не оправдала, наиболее лучшего качества звука добиться получится только при использовании натурального дерева.
Любую фанеру рассматриваемого типа с толщиной один или более миллиметра, всегда можно использовать в домашних условиях. Также, некоторые мастера могут собирать самостоятельно из нее мебель нескольких различных стилей, чем достигается красота жилищных условий.
Авиационная фанера - ее разновидности и сфера применения
Фанера охватила все сферы строительства, включая производство водного, наземного и воздушного транспорта. Но средства передвижения эксплуатируются в различных условиях. Поэтому для них применяются разные виды материалов. Так, для сооружения авиаконструкций используется авиационная фанера.
Разновидности и назначение авиационной фанеры
Фанера, используемая в самолетостроении, изготавливается из березового шпона I и II сортов, склеенного бакелитовой пленкой и/или жидкой фенолформальдегидной смолой. В зависимости от того, что было использовано для склеивания тонких пластов древесины, выделяют 4 вида фанеры:
- БП-А — листы, склеенные бакелитовой пленкой типа А.
- БП-В — листы, соединенные бакелитовой пленкой марки В.
- БС-1 — листы, склеенные жидкой фенолформальдегидной (бакелитовой) смолой.
- БПС-1В — фанера толщиной 3 мм и меньше, склеенная бакелитовой пленкой типа В, а также фанера толщиной 4 мм и больше, склеенные изнутри бакелитовой смолой, а снаружи — пленкой В.
Листы БП-А применяются для сооружения внутреннего оборудования самолетов, вертолетов и прочей воздушной технике. Марка БП-В используется в облицовочно-декоративных целях. Фанера типа БС-1 и БПС-1В обладают повышенной водостойкостью. БС-1 подходит для наружных конструкций, а БПС-1В — внутренних.
Свойства и область применения
Авиационная фанера очень легкая, прочная, но в то же время гибкая. Эти качества значительно расширили сферу ее применения, которая не ограничивается одним только самолетостроением. Материал также пригоден для производства:
- судового транспорта;
- легкового и грузового автотранспорта;
- музыкальных инструментов;
- предметов интерьера;
- коллекционных авиамоделей;
- макетов зданий.
Авиационная фанера является разновидностью бакелитовой фанеры, которую можно купить у нас. Мы гарантируем быструю доставку материала по Москве и области и организуем оптовые отправки в любую точку страны или за границу. Позвоните нам или закажите звонок на ваш телефон, чтобы узнать о нашей продукции больше.
Что такое авиационная фанера и где ее используют -
Авиационная фанера, как вытекает из ее названия, рассчитана на такие сферы производства, как самолетостроение, вагоностроение и машиностроение. Обладает этот материал особой гибкостью, высокой прочностью и небольшой плотностью. Имея малый удельный вес, авиационная фанера имеет безупречную надежность. Более подробно, что такое авиационная фанера и где ее используют, читайте в статье
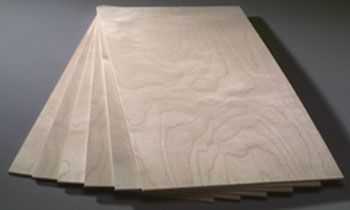
Как и из чего производят авиационную фанеру
В качестве основы авиационной фанеры служит шпон из березы. Соединен шпон в три и более слоев. Авиационная фанера выпускается толщиной от 3 до 16мм. Есть и совсем тонкие, порядка одного миллиметра.
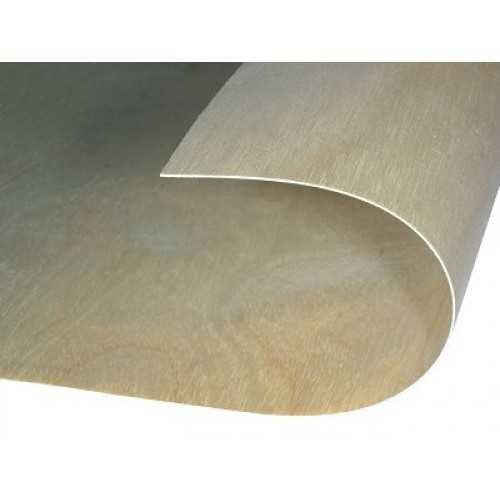
Древесные лущеные волокна, склеенные между собой:
- Обладают высокой гибкостью
- Высокой сопротивляемостью механическому воздействию
- И на фоне этих высоких показателей, обладают небольшой плотностью.
Перечисленные качества авиационной фанеры дают возможность использовать ее в машиностроении, производстве музыкальных инструментов и авиа моделировании.
Прочность, сравнимую с низколегированной сталью, авиационная фанера, получает благодаря особой технологии ее производства.
Цены на фанеру
Технология производства авиационной фанеры заключается в следующем:
Направления волокон идут перпендикулярно относительно друг друга. Каждая прослойка монтируется структурной решеткой и пересекается с последующим слоем, четко под прямым углом.
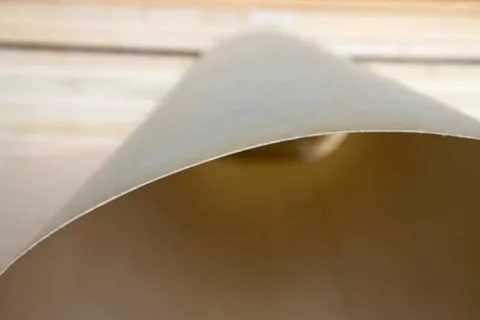
Первый слой фанеры -это ее середина. Далее слои приклеиваются сверху и снизу. Поэтому, каждый лист авиационной фанеры, состоит всегда из нечетного количества слоев шпона.
Что обозначает маркировка на листах авиационной фанеры
Один из типов маркировки авиационной фанеры, является наличие обработки ее поверхностей, а именно
- Односторонняя шлифовка листа авиационной фанеры маркируется аббревиатурой Ш1
- Аббревиатура Ш2 обозначает, соответственно, наличие шлифовки двух сторон поверхности фанеры
- Отсутствие шлифовки маркируется, как НШ
Как правило, авиационная фанера основана на березовом шпоне. Который проклеивается бакелитовым составом-с добавлением специального пластика.
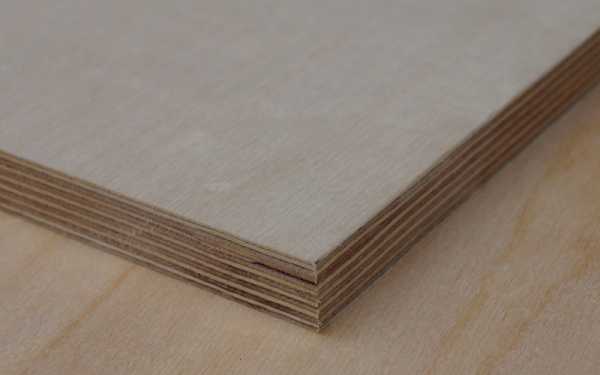
В зависимости от типа бакелитовой основы, которыми склеивается шпон, авиационная фанера подразделяется на первый и второй сорт. (маркировка А и В, соответственно).
Каких размеров производят авиационную фанеру
Раскрой и резка, а также обработка авиационной фанеры довольно сложны. Упрощается это небольшой величиной листов фанеры. Поэтому, крупногабаритных листов авиационной фанеры не встречается.
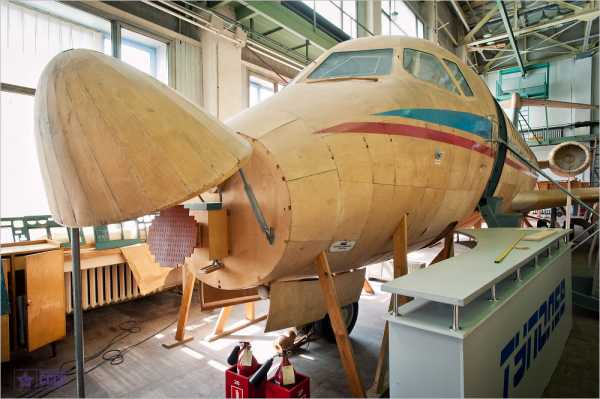
Стандартно, максимальный размер листа авиационной фанеры составляет 1525ммх1525мм. Минимальный 800ммх1525мм.
Вам будет интересно
Авиационная фанера Википедия
Дельта-древесина, или ДСП-10, или лигнофоль, или балинит — конструкционный композитный материал, древеснослоистый пластик на основе формальдегидной смолы, армированной древесными волокнами. Получался пластификацией древесного шпона (обычно берёзового) путём пропитки его фенол- или крезолоформальдегидной смолой с последующим горячим прессованием под высоким давлением.
Дельта-древесина имеет всего в два раза большую, чем обычная древесина, плотность, при этом значительно превосходя её по прочности (она выше, чем у многих алюминиевых сплавов, хотя и ниже, чем у авиационного дюралюмина после термической обработки и искусственного старения). Кроме того, этот материал практически не горюч, обладает абсолютной стойкостью к поражению грибком (гнили) и имеет длительный срок службы без потери качеств (десятки лет в неблагоприятных условиях[1]).
Дельта-древесину не следует путать с водостойкой бакелитизированной фанерой (марок ФБС, ФБС-А, ФБВ), которая представляет собой обычную фанеру с пропиткой спиртовым или водным раствором фенол-формальдегидной смолы, часто даже не на всю толщину пакета.
История
Во второй половине 1930‑х годов возможности древесины в качестве авиационного конструкционного материала оказались фактически исчерпаны — дальнейшее повышение лётных и тактико-технических характеристик боевых самолётов потребовало освоения принципиально новых материалов, имеющих более выгодное соотношение массы и прочности. Наиболее перспективны в этом отношении были высокопрочные сплавы на основе алюминия (дюралюмины), работы над применением которых в авиации были организованы в СССР ещё в начале 1920-х годов и вылились в создание серийных цельнометаллических самолётов ТБ-1, ТБ-3, ТБ-7 и других. Между тем, производство алюминия и его сплавов в стране не поспевало за быстро растущими потребностями авиации, так что наиболее массовые в советских ВВС машины — разведчики и истребители — в тридцатые годы в основном сохраняли цельнодеревянную или смешанную деревометаллическую конструкцию планера.
В предвоенные годы, в условиях назревающего масштабного военного конфликта с участием СССР, встал вопрос о резком увеличении объёмов выпуска боевых самолётов при одновременном значительном повышении их характеристик. Эта задача не могла, однако, быть решена только за счёт перехода на цельнометаллические конструкции, так как дюралюминий и другие алюминиевые сплавы всё ещё оставались остродефицитными конструкционными материалами, не хватало и металлических полуфабрикатов из легированной стали («хромансиль»), которые использовались главным образом в ферменных конструкциях, вроде моторамы. Более того — по мере увеличения объёмов выпуска начались проблемы даже с поставкой на заводы качественной древесины (до войны большая часть древесины для авиационной промышленности импортировалась, так как, несмотря на обилие лесов, из-за холодного климата отечественная древесина имеет в основном низкое качество; молодые деревья ввиду медленного роста обычно не имеют достаточного диаметра ствола, а старая древесина имеет низкие механические свойства). Невозможно было обеспечить и достаточно быструю перестройку производства на авиационных заводах, многие из которых до этого не имели опыта производства цельнометаллических конструкций — не говоря уже о расширении объёмов производства самолётов за счёт задействования предприятий иного профиля (в то время, как выпуск цельнодеревянных самолётов мог быть развёрнут в военное время на имевших практически весь необходимый набор производственного оборудования и опыт деревообработки деревообрабатывающих комбинатах и мебельных фабриках; так, Шумерлинский деревообрабатывающий комбинат в годы войны был задействован в выпуске самолетов Як-6).
Всё это подстёгивало опытные работы по применению в авиации различных древеснослоистых пластиков, или, по терминологии второй половины 1930-х годов, «облагороженной древесины» (кроме собственно дельта-древесины к этой группе материалов относились также бакелитовая фанера, балинит и другие), имевших значительно более высокие характеристики по сравнению с обычной древесиной, но при этом сходных с ней по используемым в производстве технологическим приёмам. Процесс был разработан советским авиационным инженером Леонтием Иовичем Рыжковым в 1935 году, когда он работал на Кунцевском заводе воздушных винтов[2][3]. К 1940 году он был подробно изучен и описан во Всесоюзном институте авиационных материалов Я. Д. Аврасиным[4]. Впоследствии технология её производства была усовершенствована специалистами завода «Карболит».
Дельта-древесина имела временное сопротивление растяжению 27 кг/мм², тогда как у сосны этот параметр составлял 11 кг/мм², у термически обработанного и состаренного дюралюмина Д-1А — 37 кг/мм², термически обработанного и состаренного дюралюмина Д-16 — 43 кг/мм². Такие характеристики позволяли, хотя и с некоторыми оговорками, использовать этот материал для создания боевых самолётов, удовлетворяющих имевшимся на тот момент требованиям. В частности, дельта-древесина (наряду с древесиной сосны, липы и берёзы) широко применялась в конструкции истребителя ЛаГГ-3, разработанного ОКБ-301 под руководством В. П. Горбунова. Также из неё некоторое время изготавливались части фюзеляжей и крыльев самолётов Ил и Як, некоторые детали машин и элементы производственной оснастки (для экономии металлов).
Производство
Авиационная дельта-древесина (ДСП-10) по ГОСТ 226-41 получалась путём горячего прессования березового шпона толщиной 0,5 (продольные слои) и 0,55 мм (поперечные слои), пропитанного водноспиртовым раствором феноло- или креозоло-формальдегидной смолы марок СБС-1, СКС-1 и СКС-2. Для листовой дельта-древесины толщина шпона 0,35…0,55 мм, в зависимости от толщины изготовляемого листа. После пропитки смолой и сушки шпон собирался в пакеты, причём через каждые 10 листов шпона с продольным направлением волокон один лист укладывали в поперечном направлении. Толщина пакета — в среднем 50 слоёв. Собранные пакеты закладывались между плитами гидравлического пресса и подвергались прессованию при температуре 140…150 °С и давлении до 150 кг/см² в течение порядка 3 часов (для плиты толщиной 18…20 мм). При таких температуре и давлении древесина уплотнялась практически вдвое, а смола — подвергалась полному отверждению, что придавало получаемому материалу совершенно иные свойства по сравнению с обычной древесиной. Готовый продукт содержал порядка 80 % древесных волокон, остальное — отверждённая смола и влага, до 4…6 % при приёмке и до 7 % в эксплуатации. В зависимости от физико-механических качеств, авиационная дельта-древесина подразделялась на четыре сорта — А, А1, Б и В.
Дельта-древесина поставлялась в виде коротких (1400…1600 мм) и длинных (1650…5000 мм) досок толщиной 15 или 17 мм и шириной от 200 мм, а также листов толщиной до 10 мм. В производстве могла подвергаться всем видам механической обработки на деревообрабатывающих станках при использовании резцов повышенной стойкости, склеивалась белковыми или смоляными клеями. Это обеспечило при переходе на новый материал технологическую преемственность с привычной авиазаводам обычной древесиной.
Дельта-древесина марки ДСП-10 применялась для изготовления силовых конструкций планера самолёта, в частности длинные доски сортов А, А1 и Б — для лонжеронов крыла и усиленных шпангоутов, а короткие — для комлевой части лопастей воздушных винтов. Дельта-древесина сорта В применялась для штампов, предназначенных для холодной штамповки алюминиевых и магниевых сплавов, различных вспомогательных производственных приспособлений, а также в качестве электроизоляционного материала в электроаппаратуре.
Близкими к дельта-древесине свойствами обладал так называемый балинит (ДСП-20), его также получали горячим прессованием пакета пропитанного фенол-формальдегидной смолой шпона, но при этом шпон предварительно подвергался выщелачиванию в растворе едкого натра. Балинит поставлялся в виде плит толщиной 10, 15, 20, 25, 30, 40, 50 или 60 мм, а также листов толщиной от 1 до 6 мм, содержание древесных волокон в готовом продукте — 75…80 %. Иногда имелась рубашка (наружный облицовочный слой) из бумаги или ткани. Обрабатывался аналогично дельта-древесине и считался взаимозаменяемым с ней, применялся для изготовления выравнивающих прокладок, законцовок силовых бобышек, обшивки лонжеронов, закрылков, предкрылков, щитков, лючков, плоскостей и носков стабилизатора, туннелей радиатора, гаргротов фюзеляжей, обшивки крыльев и центроплана и носков крыла и центроплана. Балинит марки ДСП-м предварительно пропитывался минеральным маслом и применялся для изготовления деталей, в ходе эксплуатации подвергающихся трению при затруднённой смазке — например, самосмазывающихся подшипников.
Применение
В наши дни дельта-древесина применяется в мебельном производстве (для деревянных узлов, испытывающих повышенные нагрузки). Ранее применялась в авиакосмической промышленности, в частности — для воздушных рулей, устанавливавшихся на блоки первой ступени ракет-носителей семейства Р7, и лопастей вертолётных рулевых винтов (производства завода «Вперёд»). В настоящее время технология производства высокосортной дельта-древесины в России утеряна, что является одной из главных причин вывода из эксплуатации вертолётов типа Ми-10 и подобных, имеющих винты из этого материала[1].
Также из дельта-древесины ранее изготавливались опорные изоляторы, преимущественно троллейбусных, изредка трамвайных, контактных сетей. Хотя такие изделия не производятся с 1970-х годов, тем не менее, их срок службы оказался достаточно велик и они до сих пор ещё массово используются в существующих контактных сетях, заменяясь постепенно стеклянными и полимерными.
В России дельта-древесина выпускается под названием «Пластик древесный слоистый» по ГОСТ 13913-78.
См. также
Примечания
Авиационная фанера: производство, маркировка и применение
Данный материал изготавливается из берёзового шпона высокого качества, имеет три или более (нечётное количество) клееных слоя и при малой плотности обладает большой гибкостью и прочностью. Так, авиационная фанера 3 мм – 16 мм или более, это уже доска – может применяться не только в авиамоделировании, но и при изготовлении музыкальных инструментов, хотя самая тонкая может иметь 1 мм.
Ниже мы поговорим по поводу гарантированных свойств конструкционного материала, его марок и областей применения, а также посмотрим демонстрацию видео в этой статье.
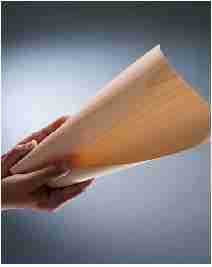
Как делают и где используют
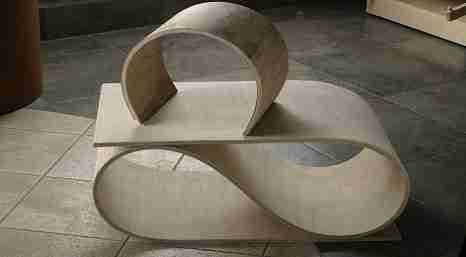
Такую продукцию можно встретить под названием дельта-древесины, что, в сущности, аналогично авиационной фанере, так как изготавливается из того же пластифицированного берёзового шпона. Перед склеиванием слоёв бакелитовым клеем их пропитывают фенолформальдегидной смолой при температуре 270⁰C под давлением 6 атмосфер. Производство такого древесного конструкционного материала производится в согласии с ГОСТ 226-41, по сортам Аи Б.
Производство и маркировка
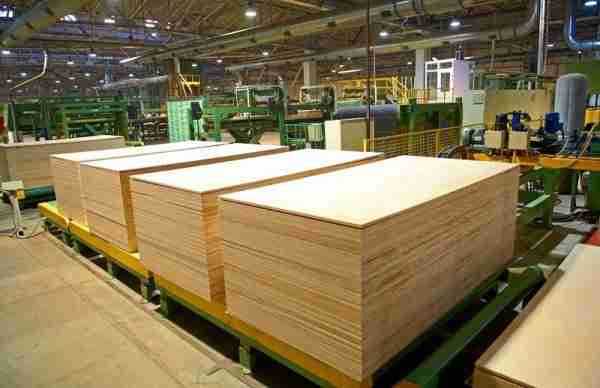
- Так, можно разделить продукцию по следующим маркам: БП-А и БП-В – это относится к фанере, которая склеена бакелитовой плёнкой типа А и В (ГОСТ 2707). А также БС-1, где шпон склеивается смолой типа СФЖ-3011 (ГОСТ 20907) и БПС-1В, где до 3 мм толщины продукция склеивается бакелитовой плёнкой типа В, а от 4 мм до 6 мм бакелитовая плёнка только снаружи, а внутри уже знакомая нам смола СФЖ-3011.
- При изготовлении такой фанеры инструкция предусматривает расположение шпона по принципу взаимной перпендикулярности. Это означает, что направления волокон каждого слоя пересекаются, образуя своеобразную структурную решётку, которая существенно повышает прочность конструкционного материала.
- Увеличение предела прочности на растягивание конструкционной древесины прямо пропорционально уменьшению её толщины и имеет для продукции 1-го сорта – 65-95 МПа и для 2-го сорта – 50-82,5 МПа. С уменьшением толщины материала также увеличивается предельная прочность на скалывание по клеевому слою после часового кипячения – она равняется 1,6-2 МПа. Допустимая шероховатость поверхности авиационной фанеры допускается не более 100 мкм при влажности 5%-9%.
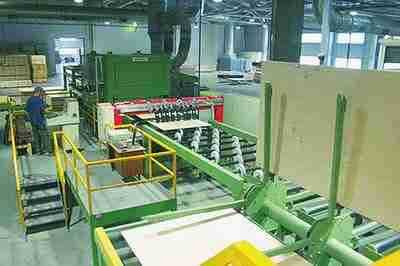
- Геометрические параметры конструкционной древесины данного типа по длине составляют от 1000 мм до 1525 мм, по ширине – от 800 мм до 1525 мм с допуском на градацию – 25 мм. Толщина листов для БП-А и БП-В – 1 мм, 2 мм, 3 мм, а вот для БС – от 1 мм до 12 мм, для БПС – от 2 мм до 6 мм.
- Так, общий формат листа для авиационной фанеры составляет: 1550х1550, 1525х1525, 1270х1270, 1220х1220. При этом, толщина листа может быть: 0,4 мм; 0,6 мм; 0,8 мм; 1,0 мм; 1,2 мм; 1,5 мм; 2,0 мм; 2,5 мм; 3,0 мм; 4,0 мм; 5,0 мм, 6,0 мм; 8,0 мм; 10 мм, 12 мм.
- Изготовление любой фанеры регулируется нормативами согласно ГОСТ 3916.1-96. Лист должен иметь только нечётное количество слоёв шпона и его волокна должны пересекаться с соседними под углом 90⁰, образуя структурную решётку. Сам производственный процесс изготовления продукции разделяется на определённые этапы, которые состоят из сортировки сырья, лущения шпона, прессования, склеивания и сушки.
- В маркировке листа могут присутствовать буквы Ш или Ш2, что означает шлифовку одной или двух сторон изделия. Низкие сорта не шлифуются и в маркировке в таких случаях стоят буквы НШ.
Рекомендация. Низкие, нешлифованные сорта фанеры с успехом можно использовать для сооружения арок, ниш и перегородок, которые дополнительно отделываются облицовочными материалами.
Применение
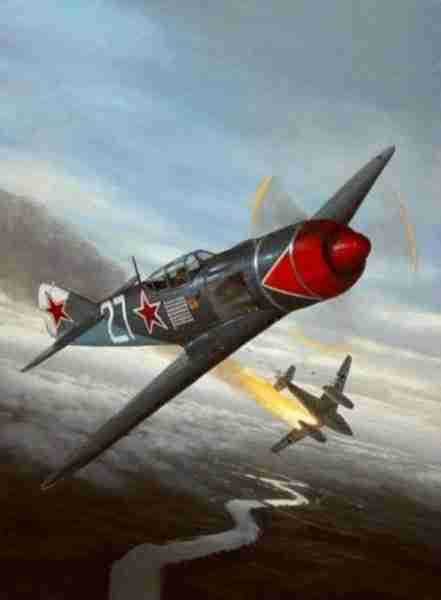
- Общеизвестным является тот факт, описываемая нами конструкционная древесина или авиамодельная фанера широко применялась именно в самолётостроении, особенно в годы Великой Отечественной Войны. Благодаря малому весу материала машина получалась лёгкой, а гибкость и прочность способствовала возможности выдерживать аэродинамические нагрузки при эксплуатации самолёта. Впрочем, авиамоделирование (особенно любительское) и сейчас не обходится без широкого применения авиационной фанеры.
- Помимо авиационной промышленности такая фанера широко используется для коллекционирования (те же модели самолётов, но так же и модели судов), так же материал широко известен в судостроении. При поиске архитектурных решений для оформления здания, района или даже города, проектировщики своими руками изготавливают макеты, на основании которых и утверждаются целые ансамбли. Также гибкая фанера очень помогает при решении нестандартных оформлений интерьера, где гипсокартон оказывается слишком непрочным.
- Было бы неправильно умолчать о производстве музыкальных инструментов (см. фото вверху), где до недавнего времени без фанеры высокого качества не обходились вообще. Ведь для любого декового инструмента нужна композиционная древесина и её замена на пластик в последние годы себя никак не оправдывает – лучшее качество звучания может быть только с натуральным деревом.
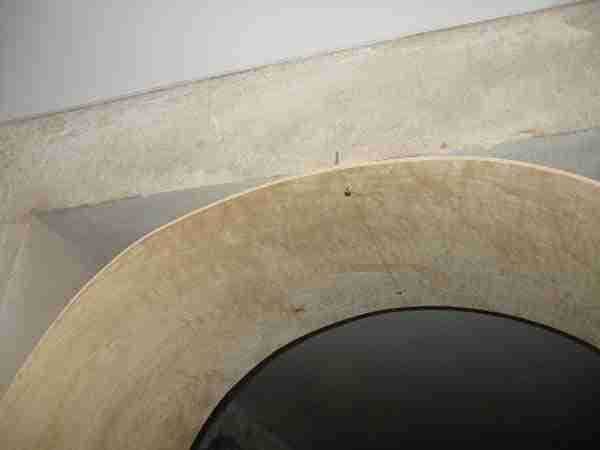
Совет. Если вы самостоятельно занимаетесь домашним ремонтом своими руками, не имея при этом профессиональных навыков, то можно использовать тонкую фанеру, например, для арок.
Хотя её цена выше, зато вы легко придадите ей любую форму, в отличие от гипсокартона, который гнётся только с применением особых технологий.
Заключение
Любая авиационная фанера — 1 мм или толще, всегда может пригодиться на бытовом уровне для ремонта и дизайнерского оформления квартиры. Кроме того, домашние умельцы могут использовать её для изготовления мебели в стиле китч, арт-декор или модерн, разнообразя тем самым свои жилищные условия.
область использования и особенности материала
Такое название авиационная фанера заслужила из-за своего прямого предназначения. Авиационная промышленность не могла бы существовать без такого конструктивного элемента, как фанера. Этот материал как никогда лучше подходит для моделирования и конструирования воздушных объектов. Авиационная фанера (3 мм) отвечает всем требованиям, выдвигаемым к материалу, и обладает необходимыми показателями гибкости, прочности и невысокой плотности.
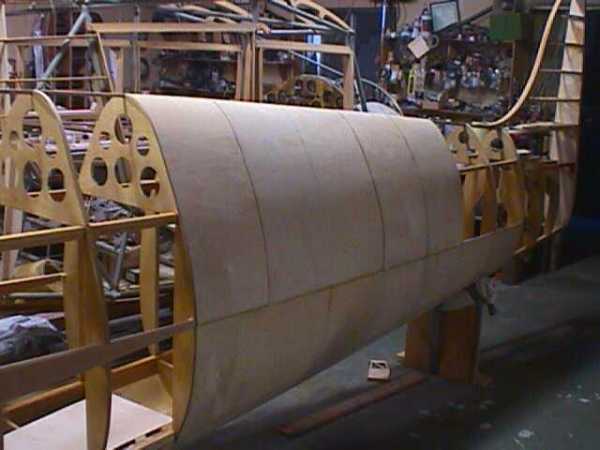
Особенности авиационной фанеры
Авиационная фанера - что это такое? Материал, который состоит из слоев березового шпона. Количество слоев определяет толщину фанеры. Минимальное их количество насчитывает три. Плотность склеивания шпона определяет прочность фанеры. Минимальная толщина фанеры для авиамоделирования - 3 мм. Этот (самый тонкий) тип фанеры встречается довольно редко. Шпон склеивается между собой при помощи бакелитовой или боскитной пленки А, B класса или специального фенольного клея.
Область применения авиационной фанеры
Гибкая авиационная фанера применяется в таких сферах деятельности человека:
- в авиапромышленности: в конструировании легких летательных аппаратов;
- при отделочных работах;
- в производстве тары;
- при изготовлении мебели;
- хендмейд: при изготовлении сувениров.
Использование авиационной фанеры позволяет в итоге сборки получить качественные изделия с гарантированными конструкционными свойствами.
Конструирование летательных аппаратов
Авиационная фанера для изготовления летательных аппаратов уникальный материал с высокими прочностными и плотностными характеристиками при минимальной толщине изделия. Изготовление выполняется согласно техническим характеристикам и полностью соответствует ГОСТу 102-75 за 1975 год.
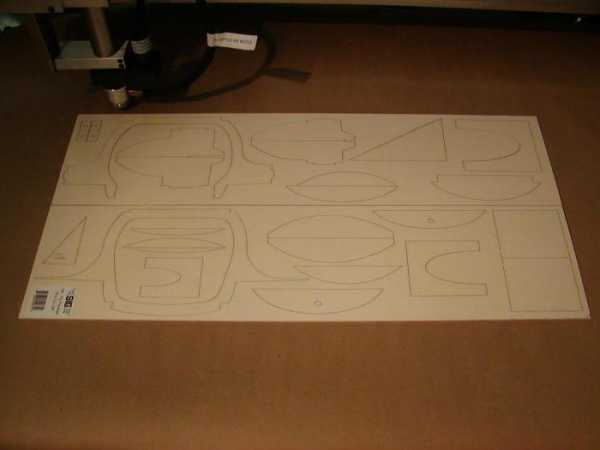
Сувениры из березовой фанеры
Для ручного изготовления сувениров зачастую используют ценные и высококачественные материалы, в том числе и фанеру. Кроме фанеры понадобятся дополнительные элементы конструирования. Для производства готовой продукции материальные и временные затраты, которые впоследствии компенсируются низким расходом базового материала и высокой стоимостью сувениров ручной работы.
Тароупаковочные материалы
Такие изделия производятся из самых дешевых видов фанеры, которая только доступна на рынке. Чаще всего используется хвойный шпон. Авиационная фанера для таких целей применяется редко. Разве что в качестве декоративных коробочек или подарочных упаковок, декорируемых росписью или гравировкой.
Мебельная промышленность
Фанера толщиною 3 мм используется для обшивки задних стенок шкафов. Такое конструирование делает конструкцию прочной и в то же время не утяжеляет ее, что позволяет легко переносить мебель при необходимости.
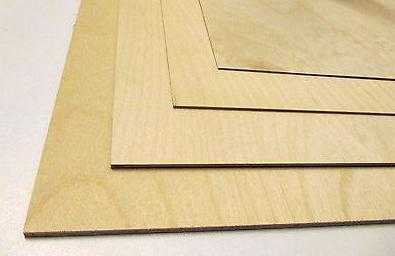
Организация отделочных работ
Трехмиллиметровая фанера активно применяется для выполнения внутренних отделочных работ потолка и стен в техпомещениях и садовых домиках. Главное преимущество такой отделки - невысокая стоимость материала и ускоренный монтаж.
Фанера – полезный и широко применяемый материал. Как видите, авиационная фанера не является узконаправленным продуктом, а используется во многих сферах деятельности человека.
Авиационная фанера Википедия
Дельта-древесина, или ДСП-10, или лигнофоль, или балинит — конструкционный композитный материал, древеснослоистый пластик на основе формальдегидной смолы, армированной древесными волокнами. Получался пластификацией древесного шпона (обычно берёзового) путём пропитки его фенол- или крезолоформальдегидной смолой с последующим горячим прессованием под высоким давлением.
Дельта-древесина имеет всего в два раза большую, чем обычная древесина, плотность, при этом значительно превосходя её по прочности (она выше, чем у многих алюминиевых сплавов, хотя и ниже, чем у авиационного дюралюмина после термической обработки и искусственного старения). Кроме того, этот материал практически не горюч, обладает абсолютной стойкостью к поражению грибком (гнили) и имеет длительный срок службы без потери качеств (десятки лет в неблагоприятных условиях[1]).
Дельта-древесину не следует путать с водостойкой бакелитизированной фанерой (марок ФБС, ФБС-А, ФБВ), которая представляет собой обычную фанеру с пропиткой спиртовым или водным раствором фенол-формальдегидной смолы, часто даже не на всю толщину пакета.
История[ | ]
Во второй половине 1930‑х годов возможности древесины в качестве авиационного конструкционного материала оказались фактически исчерпаны — дальнейшее повышение лётных и тактико-технических характеристик боевых самолётов потребовало освоения принципиально новых материалов, имеющих более выгодное соотношение массы и прочности. Наиболее перспективны в этом отношении были высокопрочные сплавы на основе алюминия (дюралюмины), работы над применением которых в авиации были организованы в СССР ещё в начале 1920-х годов и вылились в создание серийных цельнометаллических самолётов ТБ-1, ТБ-3, ТБ-7 и других. Между тем, производство алюминия и его сплавов в стране не поспевало за быстро растущими потребностями авиации, так что наиболее массовые в советских ВВС машины — разведчики и истребители — в тридцатые годы в основном сохраняли цельнодеревянную или смешанную деревометаллическую конструкцию планера.
В предвоенные годы, в условиях назревающего масштабного военного конфликта с участием СССР, встал вопрос о резком увеличении объёмов выпуска боевых самолётов при одновременном значительном повышении их характеристик. Эта задача не могла, однако, быть решена только за счёт перехода на цельнометаллические конструкции, так как дюралюминий и другие алюминиевые сплавы всё ещё оставались остродефицитными конструкционными материалами, не хватало и металлических полуфабрикатов из легированной стали («хромансиль»), которые использовались главным образом в ферменных конструкциях, вроде моторамы. Более того — по мере увеличения объёмов выпуска начались проблемы даже с поставкой на заводы качественной древесины (до войны большая часть древесины для авиационной промышленности импортировалась, так как, несмотря на обилие лесов, из-за холодного климата отечественная древесина имеет в основном низкое качество; молодые деревья ввиду медленного роста обычно не имеют достаточного диаметра ствола, а старая древесина имеет низкие механические свойства). Невозможно было обеспечить и достаточно быструю перестройку производства на авиационных заводах, многие из которых до этого не имели опыта производства цельнометаллических конструкций — не говоря уже о расширении объёмов производства самолётов за счёт задействования предприятий иного профиля (в то время, как выпуск цельнодеревянных самолётов мог быть развёрнут в военное время на имевших практически весь необходимый набор производственного оборудования и опыт деревообработки деревообрабатывающих комбинатах и мебельных фабриках; так, Шумерлинский деревообрабатывающий комбинат в годы войны был задействован в выпуске самолетов Як-6).
Всё это подстёгивало опытные работы по применению в авиации различных древеснослоистых пластиков, или, по терминологии второй половины 1930-х годов, «облагороженной древесины» (кроме собственно дельта-древесины к этой группе материалов относились также бакелитовая фанера, балинит и другие), имевших значительно более высокие характеристики по сравнению с обычной древесиной, но при этом сходных с ней по используемым в производстве технологическим приёмам. Процесс был разработан советским авиационным инженером Леонтием Иовичем Рыжковым в 1935 году, когда он работал на Кунцевском заводе воздушных винтов[2][3]. К 1940 году он был подробно изучен и описан во Всесоюзном институте
Фанера — Википедия
Схема процесса изготовления фанерыФане́ра, древе́сно-сло́истая плита́ (нем. Furnier - от франц. fournir - накладывать) — многослойный строительный материал, изготавливаемый путём склеивания специально подготовленного шпона. Для повышения прочности фанеры слои шпона накладываются так, чтобы волокна древесины каждого листа были перпендикулярны соседним, поэтому, чтобы направления внешних слоёв совпадали, количество слоёв шпона обычно нечётное: от трёх и более.
Самодельный вездеход «Каракат» с кузовом из фанерыСтроительство
Фанера называется продольной, если волокна в лицевых слоях направлены вдоль длинной стороны, в противном случае — поперечной.
Фанера из древесины как твёрдых, так и мягких пород выпускается нескольких типов и сортов, которые различаются назначением, сроком службы, внешним видом и стоимостью.
По предназначению — строительная, промышленная, упаковочная, мебельная и конструкционная.
По видам фанеру часто разделяют на два популярных вида — ФК (влагостойкая) и ФСФ (повышенной влагостойкости).
По типу обработки — ламинированная.
По внешнему виду (согласно ГОСТ 3916.1-96) (определяется количеством пороков и дефектов поверхности наружного слоя шпона): E (элита), I, II, III, IV.
По материалу, из которого изготовляется[править | править код]
- Хвойная фанера (изготавливается из шпона хвойных пород деревьев: лиственницы, сосны, пихты, ели). Иногда для изготовления фанеры используется шпон сибирского кедра — такая фанера используется в декоративных целях. Для хвойной фанеры обязательным является содержание хвойного шпона в наружных слоях — внутренние могут содержать шпон лиственных пород древесины.
- Берёзовая фанера (изготавливается из шпона берёзы) получила распространение практически во всех областях, но из-за относительно более высокой стоимости в строительстве используется не так широко, как хвойная.
- Фанера из тополя, которая производится преимущественно в Китае, существенно дешевле российских аналогов из берёзы и хвойных пород, однако уступает им по параметрам[источник не указан 994 дня].
По количеству слоёв[править | править код]
Фанерные слои- трёхслойная
- пятислойная
- многослойная
В основном листы фанеры имеют нечётное количество слоёв шпона: в этом случае шпон расположен симметрично относительно среднего слоя. Если слоёв шпона в фанере четыре, то центральные слои располагают и склеивают перпендикулярно наружным, что увеличивает общую прочность и стойкость к деформации.
По пропитке[править | править код]
Водостойкая фанера — материал, обработанный специальным образом для увеличения сопротивления влаге. Максимально увеличить влагостойкие характеристики фанеры может помочь ламинирование.
- ФБА — это листы фанеры, которые проклеены натуральным альбуминоказеиновым клеем. Преимущество фанеры ФБА в том, что она является экологически чистым строительным материалом, но её небольшая влагостойкость ограничивает применения этой марки.
- ФСФ (фанера, изготавливаемая с применением смоляного фенолформальдегидного клея). Эта фанера характеризуется относительно высокой износоустойчивостью, механической прочностью и высокой водостойкостью. ФСФ — один из самых популярных видов фанеры, используется в строительстве, производстве, кровельных работах. Допускается для применения в жилых помещениях, если класс эмиссии не превышает Е1.
- ФСФ-ТВ (фанера огнезащищённая). Обладает свойствами фанеры марки ФСФ, но не подверженная горению, относится к группе трудногорючих материалов. Применяется в пассажирском вагоностроении и промышленном/гражданском строительстве.
- ФК (фанера, получаемая при приклеивании шпонов карбамидным клеем). Обладая меньшими водостойкими характеристиками, ФК используется преимущественно при внутренней отделке помещений, в мебельном производстве, при изготовлении деревянной тары, при работе с конструкциями внутри помещения.
- ФКМ. В качестве клея при производстве фанеры ФКМ используются меламиновые и меламиноформальдегидные смолы.
- ФБ (фанера, пропитанная бакелитовым лаком, впоследствии склеивается). Этот вид обладает максимальной сопротивляемостью воздействию агрессивной среды и может использоваться в условиях тропического климата, при повышенной влажности и даже под водой.
- БС (фанера, пропитанная бакелитовым клеем, С — спирторастворимый). Эта фанера обладает уникальными свойствами — сверхвысокой прочностью, стойкостью к агрессивным средам, гибкостью, упругостью, водонепроницаема, не гниёт, не раскисает. Её ещё называют авиационная фанера за то, что раньше использовалась только в авиа- и судостроении.
- БВ (фанера, пропитанная бакелитовым клеем, В — водорастворимый). Эта фанера обладает теми же свойствами, что и фанера БС, за исключением влагостойкости, поскольку клей, применяемый при склеивании слоев, водорастворим.
По виду обработки поверхностей[править | править код]
- НШ — нешлифованная фанера.
- Ш1 — материал, шлифованный с одной стороны.
- Ш2 — материал шлифованный с двух сторон.
В настоящий момент ГОСТы предусматривают наличие пяти сортов фанеры, которые отличаются наличием и количеством допустимых дефектов обработки[2], пороков древесины и её дефектов.
Нормы ограничения пороков древесины и дефектов обработки[править | править код]
Наименование пороков древесины и дефектов обработки по ГОСТ 30427 | Фанера с наружными слоями из шпона сортов | ||||
E (элитная) | I сорт (B) | II сорт (BB) | III сорт (CP) | IV сорт (C) | |
1. Булавочные сучки | Не допускаются | Допускаются до 3-х штук на 1 м² поверхности листа | Допускаются | ||
2. Здоровые сросшиеся светлые и тёмные сучки | Не допускаются | Допускаются диаметром, мм, не более | Допускаются с трещинами шириной не более 1,5 мм | Допускаются | |
15 | 25 | ||||
в количестве на 1 м², шт., не более | |||||
5 | 10 | ||||
с трещинами шириной, мм, не более | |||||
0,5 | 1,0 | ||||
3. Частично сросшиеся, несросшиеся, выпадающие сучки, отверстия от них, червоточина | Не допускаются | Допускаются диаметром, мм, не более | |||
6 | 6 | 6 | 40 | ||
в количестве на 1 м² поверхности листа, шт., не более | без ограничения количества | ||||
3 | 6 | 10 | |||
4. Сомкнутые трещины | Не допускаются | Допускаются длиной, не более 200 мм в количестве не более 2 шт., на 1 м ширины листа | Допускаются | ||
5. Разошедшиеся трещины | Не допускаются | Допускаются длиной, мм, не более | |||
200 | 300 | без ограничения | |||
шириной, мм, не более | |||||
2 | 2 | 10 | |||
в количестве, шт., не более | |||||
2 | 2 | без ограничения | |||
при условии заделки замазками | Допускаются длиной до 600 мм, шириной до 5 мм при условии заделки замазкой | ||||
6. Светлая прорость | Не допускается | Допускается | |||
7. Тёмная прорость | Не допускается | Допускается в общем числе с нормами п. 2 настоящей таблицы | Допускается | ||
8. Отклонение в строении древесины | Допускается незначительное случайного характера, кроме тёмных глазков | Допускается | |||
9. Здоровое изменение окраски | Не допускается | Допускается не более, %, поверхности листа 5 | Допускается | ||
10. Нездоровое изменение окраски | Не допускается | Допускается | |||
11. Гниль | Не допускается | ||||
12. Наклон | Не допускается | Допускаются в общем числе с нормами п. 3 настоящей таблицы | |||
13. Нахлёстка в наружных слоях | Не допускается | Допускается длиной, мм, не более | Допускается | ||
100 | 200 | ||||
в количестве, шт., не более | |||||
1 | 2 | ||||
на 1 м ширины листа | |||||
14. Недостача шпона, дефекты кромок листа при шлифовании и обрезке | Не допускаются | Допускаются шириной, мм | |||
15. Наличие клеевой ленты | Не допускается | Допускается в нешлифованной фанере | |||
16. Просачивание клея | Не допускается | Допускается, %, не более | Допускается | ||
2 | 5 | ||||
поверхности листа | |||||
17. Царапины | Не допускаются | Допускаются | |||
18. Вмятина, отпечаток, гребешок | Не допускаются | Допускаются глубиной (высотой) в пределах значений предельных отклонений по толщине | Допускается | ||
19. Вырыв волокон | Не допускается | Допускается, %, поверхности листа, не более | Допускается | ||
5 | 15 | ||||
20. Прошлифовка | Не допускается | Допускается | |||
21. Покоробленность | В фанере толщиной до 6,5 мм не учитывается, толщиной 6,5 мм и более допускается со стрелой прогиба не более 15 мм на 1 м длины диагонали листа фанеры | ||||
22. Металлические включения | Не допускаются | Допускаются скобки из цветного металла | |||
23. Зазор в соединениях | Не допускается | Допускается шириной, мм, не более | Допускается | ||
1 | 2 | ||||
в количестве, шт., не более | |||||
1 | 1 | ||||
на 1 м ширины листа | |||||
24. Расслоение, пузыри, закорина | Не допускаются | ||||
25. Волнистость (для шлифованной фанеры), ворсистость, рябь | Не допускаются | Допускаются | |||
26. Шероховатость поверхности | Параметр шероховатости Rm по ГОСТ 7016, мкм, не более: для шлифованной фанеры — 100, для не шлифованной — 200 | ||||
27. Вставки из древесины | Не допускаются | Допускаются при заделке в количестве, шт., не более | |||
8 на 1 м2листа | без ограничения | ||||
28. Двойная вставка | Не допускается | Допускается, шт., не более 2 на 1 м² листа | Допускается без ограничения | ||
Примечания: 1. Норма дефекта обработки «недостача шпона» относится и к внутренним слоям фанеры. |
Общими словами:
- сорт Е (элита). Дефекты не допускаются, кроме незначительных изменений случайного характера в строении древесины;
- сорт I. Максимальная длина покоробленности или трещин для фанеры первого сорта не должна превышать 20 мм;
- сорт II. Допускаются трещины до 200 мм, вставки из древесины, просачивание клея площадью до 2 % от общей площади листа фанеры;
- сорт III. Допускаются червоточины до 10 штук на квадратный метр при диаметре каждой не более 6 мм; общее количество перечисленных пороков не может быть больше 9;
- сорт IV. Фанера 4-го сорта является крайне низкокачественной. Такая фанера может иметь следующие пороки: частично сросшиеся и выпавшие сучки — без ограничения; червоточины диаметром до 40 мм без ограничения; дефекты кромок листа глубиной до 5 мм;
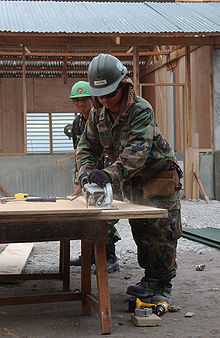
В технологическом процессе производства фанеры можно ориентировочно выделить 14 этапов:
1) Подготовка сырья к лущению.
На начальном этапе происходит отбор качественного берёзового фанерного кряжа, он должен соответствовать ГОСТу 9462-88. По поступлении на завод сырьё гидротермически обрабатывается в варочных бассейнах.
2) Окорка сырья.
Окорка — удаление с поверхности кряжа коры и луба. После произведения окорки бревна прогоняют через специальный сканер, определяющий кубатуру кряжа.
3) Разделка фанерного сырья.
Для разделки сырья на чураки используется пильный агрегат, работающий в полуавтоматическом режиме. Получившиеся от разделки под определённую ширину листа отходы отправляются в отделение переработки отходов, а сырьё в виде чураков — в приёмник-накопитель и на следующий этап, к лущильному станку.
4) Лущение, рубка и укладка шпона.
Для лущения шпона используются лущильные станки, а рубка по размерам осуществляется ножницами, получаемый шпон в сыром виде на выходе имеет толщину в 1,15—1,18 мм. Получившаяся после лущения лента шпона подаётся к пневматическим ножницам, для раскроя на форматные листы в полуавтоматическом режиме. Лущёный шпон стопками подаётся к сушилке.
5) Сушка шпона.
Сушится шпон с использованием газовых роликовых сушилок, работающих на топочных газах, а также и в термомасляной сушилке.
6) Сортировка шпона.
После сушки шпон делится на несколько частей, одна из которых направляется на ребросклеивание и шпонопочинку, а другая — сразу на сортировку в соответствии с требованиями ГОСТ 3916.1-96 или требованиями заказчика. Неформатный, кусковой и оставшийся от обрезки шпон отправляется на ребросклеивание вдоль волокон на внутренние слои, а после обрезки поперёк — на линию усовки.
7) Склеивание шпона на «ус».
Склеенный на «ус» поперёк волокон шпон идёт на внутренние слои большеформатной фанеры.
8) Ребросклеивание шпона.
Для ребросклейки используются станки с подачей шпона вдоль и поперёк древесных волокон.
9) Починка шпона.
В починку шпона идут полоски шпона шириной до 49 мм, они подбираются по направлению волокон, цвету и породе древесины, толщине относительно требующих починки листов и плотно держатся в шпоне.
10) Приготовление и нанесение клея.
Рецептура приготовления клея — секрет производства любого фанерного завода, а наносится клей на шпон клеенаносящими станками, с помощью рифлёных металлических барабанов строго цилиндрической формы.
11) Сборка пакетов.
Шпон с нанесенным клеем отправляют в наборку, где собираются пакеты, которые, проходя холодную подпрессовку, формируют будущие листы фанеры. Пакеты собираются в угольник, прижимаясь к упорам с двух сторон наборного стола. После холодной подпрессовки пакеты отправляют в загрузку горячего пресса.
12) Склеивание фанеры.
Для склеивания фанеры используется горячий гидравлический пресс с электронной системой управления прессованием, механической загрузкой и выгрузкой. После пресса фанера развозится погрузчиком в стопы для выстройки. Стопы держатся в течение 24 часов в условиях цеха чтобы снять внутренние напряжения.
13) Обрезка фанеры и шлифование.
В обрезке фанеры используются форматно-обрезные станки, а после обрезки её автопогрузчиком подают на сортировку или шлифовальный станок.
14) Сортировка, маркировка и упаковка.
Фанера подается на сортировочные площадки после обрезки и шлифования, где сортируется по ГОСТу 3916.1-96, после чего производится маркировка листов фанеры, упаковка её в стандартные транспортировочные пачки и маркировка пачек.
Производство в России[править | править код]
Фанера в России выпускается следующих основных форматов 1525×1525, 1220×2440, 2440×1220, 1250×2500, 2500×1250, 1500×3000, 3000×1500, 1525×3050 и 3050×1525 мм. Различие в расположении длины и ширины относительно формата фанеры обозначает продольное или поперечное расположение волокон шпона по длинной стороне и указывает, что если формат заявлен как 1220×2440 мм, то расположение слоёв шпона поперечное, а если 2440×1220 мм — продольное. Фанера с продольным расположением волокон шпона используется там, где требуется гибкость, а с поперечным — там, где требуется высокая жёсткость при изгибе.
Производство фанеры в России (млн. м³):
- 2002 г. — 1,8;
- 2003 г. — 2,0;
- 2004 г. — 2,2;
- 2005 г. — 2,6;
Фанерное производство в России расположено по большей части в привязке к регионам, богатым лесными ресурсами. Основная доля выпуска приходится на предприятия Северо-Западного федерального округа — около 35 % в общем объёме производства.
В России наибольшее распространение получило производство березовой фанеры (95% производства) в связи с особенностями состава лесов (из 63 фанерных заводов 62 производят березовую фанеру). Березовая фанера составляет 3-4% от мирового рынка фанеры
В 2005 году экспорт составил 1,5 млн м³, то есть около 60 % всей произведённой в стране фанеры.
- Григорьев М. А. Материаловедение для столяров, плотников и паркетчиков: Учебное пособие для ПТУ. — М.: Высшая школа, 1989. — 223 с. — 100 000 экз. — ISBN 5-06-000345-0.
- ГОСТ 3916.1-96 Фанера общего назначения с наружными слоями из шпона лиственных пород.
- ГОСТ 3916.2-96 Фанера общего назначения с наружными слоями из шпона хвойных пород.
- ГОСТ 13913-78 (ГОСТ на ДСП)
- ГОСТ 102-75 Фанера берёзовая авиационная.
- ГОСТ В-226-41 Дельта-древесина авиационная.
- Фанера // Товарный словарь / И. А. Пугачёв (главный редактор). — М.: Государственное издательство торговой литературы, 1960. — Т. IX. — Стб. 8—13
- Черкасов И. К. Фанера // БСЭ
Дельта-древесина — Википедия
Дельта-древесина, или ДСП-10, или лигнофоль, или балинит — конструкционный композитный материал, древеснослоистый пластик на основе формальдегидной смолы, армированной древесными волокнами. Получался пластификацией древесного шпона (обычно берёзового) путём пропитки его фенол- или крезолоформальдегидной смолой с последующим горячим прессованием под высоким давлением.
Дельта-древесина имеет всего в два раза большую, чем обычная древесина, плотность, при этом значительно превосходя её по прочности (она выше, чем у многих алюминиевых сплавов, хотя и ниже, чем у авиационного дюралюмина после термической обработки и искусственного старения). Кроме того, этот материал практически не горюч, обладает абсолютной стойкостью к поражению грибком (гнили) и имеет длительный срок службы без потери качеств (десятки лет в неблагоприятных условиях[1]).
Дельта-древесину не следует путать с водостойкой бакелитизированной фанерой (марок ФБС, ФБС-А, ФБВ), которая представляет собой обычную фанеру с пропиткой спиртовым или водным раствором фенол-формальдегидной смолы, часто даже не на всю толщину пакета.
Во второй половине 1930‑х годов возможности древесины в качестве авиационного конструкционного материала оказались фактически исчерпаны — дальнейшее повышение лётных и тактико-технических характеристик боевых самолётов потребовало освоения принципиально новых материалов, имеющих более выгодное соотношение массы и прочности. Наиболее перспективны в этом отношении были высокопрочные сплавы на основе алюминия (дюралюмины), работы над применением которых в авиации были организованы в СССР ещё в начале 1920-х годов и вылились в создание серийных цельнометаллических самолётов ТБ-1, ТБ-3, ТБ-7 и других. Между тем, производство алюминия и его сплавов в стране не поспевало за быстро растущими потребностями авиации, так что наиболее массовые в советских ВВС машины — разведчики и истребители — в тридцатые годы в основном сохраняли цельнодеревянную или смешанную деревометаллическую конструкцию планера.
В предвоенные годы, в условиях назревающего масштабного военного конфликта с участием СССР, встал вопрос о резком увеличении объёмов выпуска боевых самолётов при одновременном значительном повышении их характеристик. Эта задача не могла, однако, быть решена только за счёт перехода на цельнометаллические конструкции, так как дюралюминий и другие алюминиевые сплавы всё ещё оставались остродефицитными конструкционными материалами, не хватало и металлических полуфабрикатов из легированной стали («хромансиль»), которые использовались главным образом в ферменных конструкциях, вроде моторамы. Более того — по мере увеличения объёмов выпуска начались проблемы даже с поставкой на заводы качественной древесины (до войны большая часть древесины для авиационной промышленности импортировалась, так как, несмотря на обилие лесов, из-за холодного климата отечественная древесина имеет в основном низкое качество; молодые деревья ввиду медленного роста обычно не имеют достаточного диаметра ствола, а старая древесина имеет низкие механические свойства). Невозможно было обеспечить и достаточно быструю перестройку производства на авиационных заводах, многие из которых до этого не имели опыта производства цельнометаллических конструкций — не говоря уже о расширении объёмов производства самолётов за счёт задействования предприятий иного профиля (в то время, как выпуск цельнодеревянных самолётов мог быть развёрнут в военное время на имевших практически весь необходимый набор производственного оборудования и опыт деревообработки деревообрабатывающих комбинатах и мебельных фабриках; так, Шумерлинский деревообрабатывающий комбинат в годы войны был задействован в выпуске самолетов Як-6).
Всё это подстёгивало опытные работы по применению в авиации различных древеснослоистых пластиков, или, по терминологии второй половины 1930-х годов, «облагороженной древесины» (кроме собственно дельта-древесины к этой группе материалов относились также бакелитовая фанера, балинит и другие), имевших значительно более высокие характеристики по сравнению с обычной древесиной, но при этом сходных с ней по используемым в производстве технологическим приёмам. Процесс был разработан советским авиационным инженером Леонтием Иовичем Рыжковым в 1935 году, когда он работал на Кунцевском заводе воздушных винтов[2][3]. К 1940 году он был подробно изучен и описан во Всесоюзном институте авиационных материалов Я. Д. Аврасиным[4]. Впоследствии технология её производства была усовершенствована специалистами завода «Карболит».
Дельта-древесина имела временное сопротивление растяжению 27 кг/мм², тогда как у сосны этот параметр составлял 11 кг/мм², у термически обработанного и состаренного дюралюмина Д-1А — 37 кг/мм², термически обработанного и состаренного дюралюмина Д-16 — 43 кг/мм². Такие характеристики позволяли, хотя и с некоторыми оговорками, использовать этот материал для создания боевых самолётов, удовлетворяющих имевшимся на тот момент требованиям. В частности, дельта-древесина (наряду с древесиной сосны, липы и берёзы) широко применялась в конструкции истребителя ЛаГГ-3, разработанного ОКБ-301 под руководством В. П. Горбунова. Также из неё некоторое время изготавливались части фюзеляжей и крыльев самолётов Ил и Як, некоторые детали машин и элементы производственной оснастки (для экономии металлов).
Авиационная дельта-древесина (ДСП-10) по ГОСТ 226-41 получалась путём горячего прессования березового шпона толщиной 0,5 (продольные слои) и 0,55 мм (поперечные слои), пропитанного водноспиртовым раствором феноло- или креозоло-формальдегидной смолы марок СБС-1, СКС-1 и СКС-2. Для листовой дельта-древесины толщина шпона 0,35…0,55 мм, в зависимости от толщины изготовляемого листа. После пропитки смолой и сушки шпон собирался в пакеты, причём через каждые 10 листов шпона с продольным направлением волокон один лист укладывали в поперечном направлении. Толщина пакета — в среднем 50 слоёв. Собранные пакеты закладывались между плитами гидравлического пресса и подвергались прессованию при температуре 140…150 °С и давлении до 150 кг/см² в течение порядка 3 часов (для плиты толщиной 18…20 мм). При таких температуре и давлении древесина уплотнялась практически вдвое, а смола — подвергалась полному отверждению, что придавало получаемому материалу совершенно иные свойства по сравнению с обычной древесиной. Готовый продукт содержал порядка 80 % древесных волокон, остальное — отверждённая смола и влага, до 4…6 % при приёмке и до 7 % в эксплуатации. В зависимости от физико-механических качеств, авиационная дельта-древесина подразделялась на четыре сорта — А, А1, Б и В.
Дельта-древесина поставлялась в виде коротких (1400…1600 мм) и длинных (1650…5000 мм) досок толщиной 15 или 17 мм и шириной от 200 мм, а также листов толщиной до 10 мм. В производстве могла подвергаться всем видам механической обработки на деревообрабатывающих станках при использовании резцов повышенной стойкости, склеивалась белковыми или смоляными клеями. Это обеспечило при переходе на новый материал технологическую преемственность с привычной авиазаводам обычной древесиной.
Дельта-древесина марки ДСП-10 применялась для изготовления силовых конструкций планера самолёта, в частности длинные доски сортов А, А1 и Б — для лонжеронов крыла и усиленных шпангоутов, а короткие — для комлевой части лопастей воздушных винтов. Дельта-древесина сорта В применялась для штампов, предназначенных для холодной штамповки алюминиевых и магниевых сплавов, различных вспомогательных производственных приспособлений, а также в качестве электроизоляционного материала в электроаппаратуре.
Близкими к дельта-древесине свойствами обладал так называемый балинит (ДСП-20), его также получали горячим прессованием пакета пропитанного фенол-формальдегидной смолой шпона, но при этом шпон предварительно подвергался выщелачиванию в растворе едкого натра. Балинит поставлялся в виде плит толщиной 10, 15, 20, 25, 30, 40, 50 или 60 мм, а также листов толщиной от 1 до 6 мм, содержание древесных волокон в готовом продукте — 75…80 %. Иногда имелась рубашка (наружный облицовочный слой) из бумаги или ткани. Обрабатывался аналогично дельта-древесине и считался взаимозаменяемым с ней, применялся для изготовления выравнивающих прокладок, законцовок силовых бобышек, обшивки лонжеронов, закрылков, предкрылков, щитков, лючков, плоскостей и носков стабилизатора, туннелей радиатора, гаргротов фюзеляжей, обшивки крыльев и центроплана и носков крыла и центроплана. Балинит марки ДСП-м предварительно пропитывался минеральным маслом и применялся для изготовления деталей, в ходе эксплуатации подвергающихся трению при затруднённой смазке — например, самосмазывающихся подшипников.
В наши дни дельта-древесина применяется в мебельном производстве (для деревянных узлов, испытывающих повышенные нагрузки). Ранее применялась в авиакосмической промышленности, в частности — для воздушных рулей, устанавливавшихся на блоки первой ступени ракет-носителей семейства Р7, и лопастей вертолётных рулевых винтов (производства завода «Вперёд»). В настоящее время технология производства высокосортной дельта-древесины в России утеряна, что является одной из главных причин вывода из эксплуатации вертолётов типа Ми-10 и подобных, имеющих винты из этого материала[1].
Также из дельта-древесины ранее изготавливались опорные изоляторы, преимущественно троллейбусных, изредка трамвайных, контактных сетей. Хотя такие изделия не производятся с 1970-х годов, тем не менее, их срок службы оказался достаточно велик и они до сих пор ещё массово используются в существующих контактных сетях, заменяясь постепенно стеклянными и полимерными.
В России дельта-древесина выпускается под названием «Пластик древесный слоистый» по ГОСТ 13913-78.
Авиационная фанера - это... Что такое Авиационная фанера?
- Авиационная фанера
-
60. Авиационная фанера
Е. Aircraft plywood
F. Contreplaque pour les avions
Фанера для применения в авиационной промышленности
Словарь-справочник терминов нормативно-технической документации. academic.ru. 2015.
- Авиационная управляющая система
- авиационно-техническое имущество
Смотреть что такое "Авиационная фанера" в других словарях:
авиационная фанера — Фанера для применения в авиационной промышленности. [ГОСТ 15812 87] Тематики древесина клееная слоистая EN aircraft plywood FR contreplaque pour les avions … Справочник технического переводчика
Фанера — – слоистая клееная древесина, состоящая из склеенных между собой трех и более листов лущеного шпона с взаимно перпендикулярным расположением волокон древесины в смежных слоях. [ГОСТ 15812 87] Рубрика термина: Фанера Термины рубрики: Фанера… … Энциклопедия терминов, определений и пояснений строительных материалов
Фанера авиационная — – фанера для применения в авиационной промышленности. [ГОСТ 15812 87] Рубрика термина: Фанера Рубрики энциклопедии: Абразивное оборудование, Абразивы, Автодороги, Автотехника … Энциклопедия терминов, определений и пояснений строительных материалов
Фанера — У этого термина существуют и другие значения, см. Фанера (значения). Фанера … Википедия
ГОСТ 15812-87: Древесина клееная слоистая. Термины и определения — Терминология ГОСТ 15812 87: Древесина клееная слоистая. Термины и определения оригинал документа: Contreplaque a fil en long, contreplaque en long 53 Определения термина из разных документов: Contreplaque a fil en long, contreplaque en long… … Словарь-справочник терминов нормативно-технической документации
Веломобиль — «Leiba» … Википедия
Лигерад — Украинский переднеприводной лигерад конструкции И. Седлаковича с подвижной педальной кареткой и подвеской обоих колес, 2012 год. Лигерад (нем. Liegerad … Википедия
102 — ГОСТ 102{ 75} Фанера березовая авиационная. Технические условия. ОКС: 79.060.10 КГС: К24 Фанера и фанерные изделия Взамен: ГОСТ 102 49 Действие: С 01.01.76 Изменен: ИУС 10/78, 9/83, 1/85, 11/90 Примечание: переиздание 1996; см. также в сб. Фанера … Справочник ГОСТов
79.060.10 — Фанера ГОСТ 99 96 Шпон лущеный. Технические условия. Взамен ГОСТ 99 89 ГОСТ 102 75 Фанера березовая авиационная. Технические условия. Взамен ГОСТ 102 49 ГОСТ 2977 82 Шпон строганый. Технические условия. Взамен ГОСТ 2977 77 ГОСТ 3916.1 96 Фанера… … Покажчик національних стандартів
Дельта-древесина — или бакелитовая фанера конструкционный материал, получаемый пластификацией древесного шпона (обычно берёзового) путём пропитки его феноло или крезоло формальдегидной смолой под давлением порядка 6 атмосфер и температуре 270 °С, а затем… … Википедия
Фанера - вопросы и ответы
Генадий 03.08.2018
Авиационная фанера: что это такое и где применяется?
СМОТРЕТЬ ОТВЕТСтанислав 18.09.2018
Вреден ли дым, выделяемый лазером при резке фанеры?
СМОТРЕТЬ ОТВЕТГенадий 03.08.2018
Вредна ли ламинированная фанера для применения внутри помещений?
СМОТРЕТЬ ОТВЕТСтанислав 18.09.2018
Какая бывает ламинированная фанера, чем можно заменить?
СМОТРЕТЬ ОТВЕТГенадий 03.08.2018
Какой сорт фанеры использовать под линолеум?
СМОТРЕТЬ ОТВЕТСтанислав 18.09.2018
Какой стандартный размер березовой фанеры?
СМОТРЕТЬ ОТВЕТСтанислав 18.09.2018
Какую фанеру использовать для лазерной резки?
СМОТРЕТЬ ОТВЕТДмитрий 07.05.2018
Какую фанеру лучше использовать для опалубки?
СМОТРЕТЬ ОТВЕТСергей 25.02.2018
Можно ли использовать фанеру ФСФ в жилых зданиях?
СМОТРЕТЬ ОТВЕТСтанислав 18.05.2018
Отличие фанеры от ДСП: что лучше, экологичнее, прочнее, легче, дешевле?
СМОТРЕТЬ ОТВЕТДмитрий 19.05.2018
Чем лучше пилить фанеру в домашних условиях?
СМОТРЕТЬ ОТВЕТДмитрий 19.05.2018
Чем отличается бакелитовая фанера от ламинированной?
СМОТРЕТЬ ОТВЕТДмитрий 19.05.2018
Что лучше влагостойкая фанера или влагостойкая ДСП?
СМОТРЕТЬ ОТВЕТЕвгений 19.05.2018
Что лучше использовать на стены: фанеру или ОСБ?
СМОТРЕТЬ ОТВЕТЕвгений 19.05.2018
Что лучше стелить на пол под линолеум: ОСБ или фанеру?
СМОТРЕТЬ ОТВЕТЕвгений 19.05.2018
Что лучше: фанера, ОСБ или ДСП – чем отличаются материалы?
СМОТРЕТЬ ОТВЕТГенадий 03.08.2018
Что такое сорт фанеры, какие они бывают и чем отличаются?
СМОТРЕТЬ ОТВЕТЕвгений 19.05.2018
Что экологичнее и безопаснее для здоровья: фанера или ОСБ-плита?
СМОТРЕТЬ ОТВЕТ